Dzięki zleceniom produkcyjnym wiadomo co będzie realizowane na produkcji - jakie wyroby, w jakim czasie, na jakich liniach, a nawet na rzecz jakiego zamówienia czy kontrahenta. Zlecenia stanowią wyznacznik planu - w zależności od tego jaką przyjmujesz zasadę planowania - będziesz mógł raportować wykonanie całego zlecenia, albo poszczególnych operacji wchodzących w jego skład. Poniższy opis, mam nadzieję, wyjaśni Ci wszelkie wątpliwości odnośnie wykorzystania zleceń i przybliży Ci zasadę działania.
Zlecenia produkcyjne widoczne są w dwóch miejscach:
- Planowanie > Zlecenia produkcyjne
- Planowanie > Planowanie zleceń
różnica jest drobna, ale może mieć dla Ciebie spore znaczenie. Lista “Zlecenia produkcyjne” zawiera wszystkie zlecenia jakie kiedykolwiek do systemu wprowadziłeś, również te zakończone i odrzucone. Lista “Planowanie zleceń” zawiera informacje tylko o tych otwartych zleceniach. Przy bieżącej pracy zatem wydaje się, że planowanie zleceń jest wygodniejszym widokiem - nie zaśmiecasz listy zleceniami już ukończonymi lub takimi, które nie będą przekazywane na działy.
Zanim zaczniesz pracę ze zleceniami przejrzyj parametry i skonfiguruj działanie wg swoich potrzeb.
Dodanie zlecenia produkcyjnego
Zlecenie produkcyjne może być dodane na kilka różnych sposobów - wypróbuj każdy z nich. Zobaczysz, że efekt jest taki sam - istniejące zlecenie, które możesz przekazać na produkcję. Zlecenie produkcyjne możesz dodać:
- ręcznie,
- z poziomu zamówienia sprzedaży (pojedynczo i zbiorowo),
- z poziomu produktu,
- przez wygenerowanie zleceń na komponenty,
- przy okazji dodania grupy zleceń,
- poprzez import z pliku .xlsx.
Poniżej znajdziesz szczegółowy opis każdej z tych metod.
Dodanie ręczne zlecenia produkcyjnego
Aby ręcznie dodać zlecenie produkcyjne kliknij
Dodaj nowy
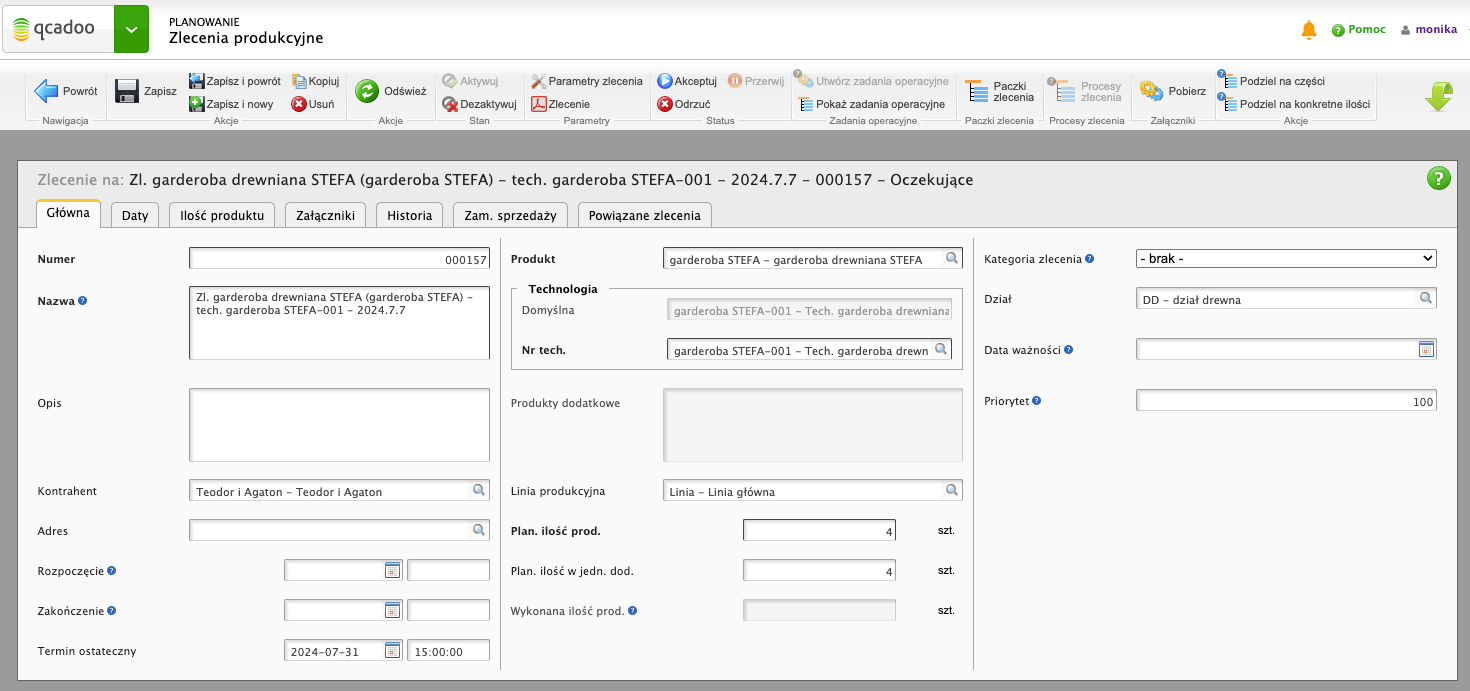
Rozpocznij od wskazania produktu i planowanej ilość. Jeśli produkt ma zdefiniowaną, oprócz jednostki podstawowej, jednostkę dodatkową i przelicznik między nimi, odpowiednio wyliczy się ilość w jednostce dodatkowej w zleceniu.
Na podstawie produktu uzupełnimy jego zaakceptowaną domyślną technologię. Możesz ją zmienić na inną zaakceptowaną - technologia wzorcowa pozostanie niezmieniona, a nowo wskazana będzie technologią, na podstawie której będzie realizowana produkcja.
Na podstawie technologii uzupełni się:
- nazwa zlecenia,
- linia produkcyjna - na podstawie linii podanej w zasięgu technologii (gdy zasięg = 1 dział). Jeśli linia produkcyjna w technologii nie jest podana, zostanie uzupełniona na podstawie domyślnej linii z parametrów,
- produkty dodatkowe - jeśli zostały ujęte w produktach wyjściowych,
- dział - na podstawie działu podanego w zasięgu technologii (gdy zasięg = 1 dział). Jeśli działu nie ma w technologii, to uzupełnimy dział przypisany do linii uzupełnionej z wartości domyślnych określonych w parametrach,
- opis - jeśli parametr Uzupełniaj opis zlecenia na podstawie opisu technologii jest zaznaczony.
Traktuj te dane jako wartości domyślne - możesz je zmienić na etapie rozpisywania zlecenia.
W zleceniu możesz uzupełnić ponadto:
- kontrahenta - z uprzednio zdefiniowanej listy firm i jego adres dostawy,
- datę rozpoczęcia,
- datę zakończenia,
- termin ostateczny - poinformujemy Cię o ewentualnym przekroczeniu tego terminu,
- kategorię zlecenia - do wyboru ze słownika kategorii. Wykorzystaj to pole do oznaczania / grupowania zleceń wg własnych preferencji. Np. że zlecenie jest pilne.
- priorytet - informuje o tym jak ważne jest dla Ciebie to zamówienie. Im mniejsza liczba, bym istotniejsze i tym szybciej chcesz je zrealizować. Domyślnie każde zlecenie otrzymuje priorytet = 100.
Po wypełnieniu danych w zakładce Główna zapisz zlecenie używając przycisku
Zapisz.
Zlecenie otrzymuje status Oczekujące (więcej o statusach zlecenia przeczytasz tutaj). Na tym etapie możesz je dowolnie zmieniać. Możesz je też usunąć jeśli uznasz, że nie jest Ci potrzebne.
Utworzone zlecenie produkcyjne możesz powiązać z zamówieniem sprzedaży - zachowując tym samym informację o tym na rzecz jakiego zgłoszenia klienckiego pracujecie. Aby tak się stało wskaż w zleceniu produkcyjnym w zakładce Zam. sprzedaży utworzone wcześniej zamówienie. Możesz również skorzystać z opcji tworzenia zleceń z poziomu zamówienia sprzedaży.
Dodanie zlecenia z poziomu zamówienia sprzedaży
Masz już zaewidencjonowane zamówienie sprzedaży. Wiesz zatem co potrzebuje klient. Możesz wykorzystując zamówienie utworzyć zlecenie produkcyjne. I tu masz znowu kilka możliwości:
- tworzenie zleceń do każdej zamówionej pozycji z osobna,
- tworzenie zleceń do wielu zaznaczonych pozycji zamówionych (z poziomu pojedynczego zamówienia i z poziomu listy pozycji zamówień sprzedaży). Z dodatkową opcją tworzenia zbiorczych zleceń,
- tworzenie zleceń poprzez utworzenie grupy zleceń do zamówienia.
Ze szczegółami zapoznasz się w tym i tym rozdziale dokumentacji o zamówieniach sprzedaży.
Dodanie zlecenia z poziomu produktu
Dodanie zlecenia z poziomu produktu będzie przydatne w sytuacji, gdy produkujesz na magazyn i zlecasz wiele produktów na raz w takiej samej ilości. Zamiast tworzyć każde zlecenie ręcznie, możesz zaznaczyć produkty, które będziesz produkować i utworzyć je zbiorczo poprzez wywołanie funkcji.
Wejdź w produkty > produkty i zaznacz te, które chcesz zlecić:
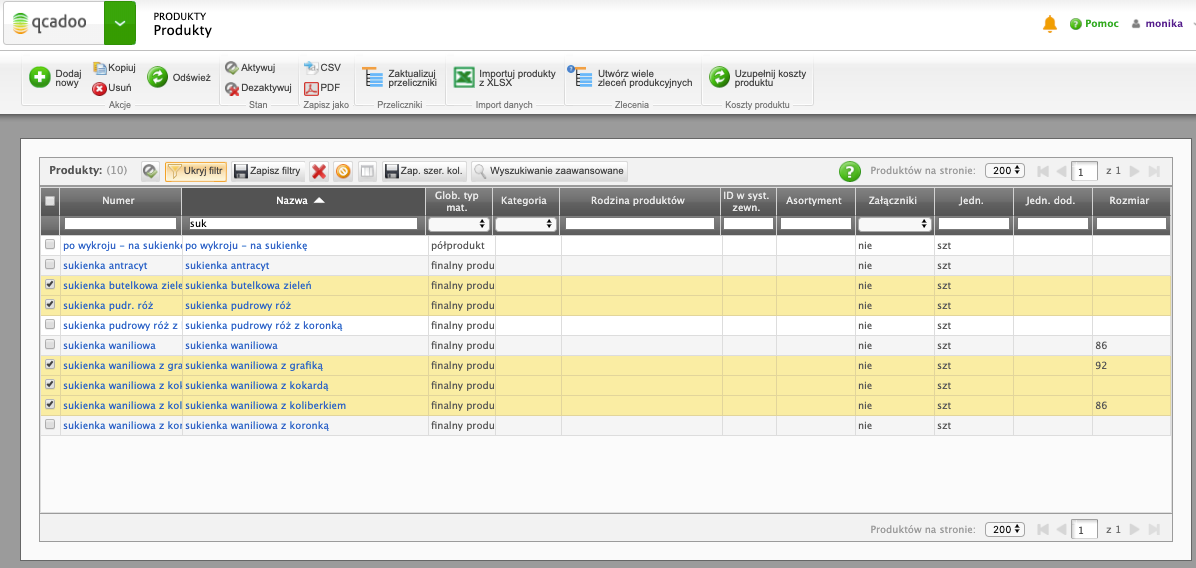
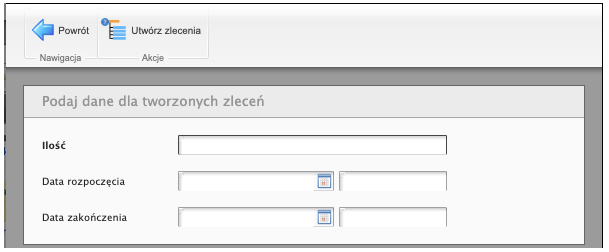
Następnie kliknij przycisk
Utwórz wiele zleceń produkcyjnych. W uruchomionym oknie podaj ilość - wszystkie dodane zlecenia produkcyjne będą miały taką samą planowaną ilość. Możesz też podać datę rozpoczęcia i datę zakończenia, ale nie jest to konieczne.
Aby wygenerować zlecenia kliknij przycisk
Utwórz zlecenia.
Jeśli wszystko się powiedzie utworzonych zostanie tyle zleceń ile zaznaczonych produktów. Aby w pełni korzystać z tej funkcjonalności zadbaj o to, by były stworzone technologie zaakceptowane i domyślne. To na podstawie technologii uzupełniamy większość danych w zleceniu.
Zlecenia na komponenty
No właśnie - wspomniane zostały zlecenia na komponenty. Czym są? Zlecenia na komponenty to powiązane zlecenia, wygenerowane automatycznie, na półprodukty niezbędne do realizacji zlecenia głównego. Podstawą do generowania zleceń w ten sposób jest odpowiednio utworzona technologia - ze szczegółami zaznajomisz się tutaj.
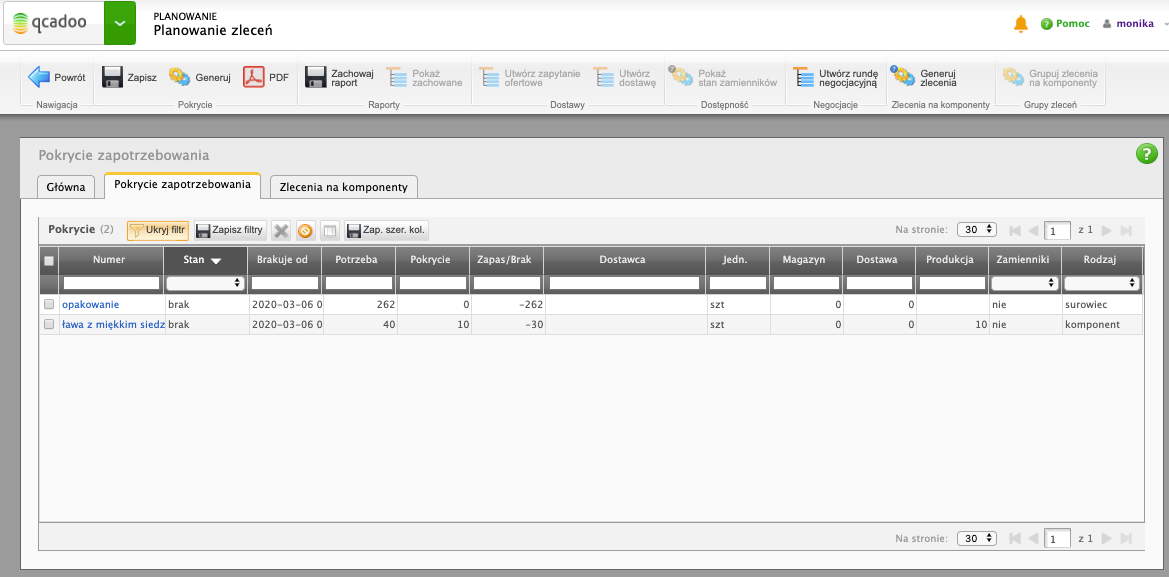
Jakie są plusy stosowania tego podejścia do produkcji?
- możesz zlecać produkcję półproduktów tylko wtedy, gdy faktycznie nie masz ich na stanie. Gdy są dostępne (bo np. zostały z poprzedniego zlecenia), to program nie wygeneruje zlecenia i będziesz mógł pobrać produkt ze stanu
- możesz podzielić produkcję na etapy i część pracy wykonywać dużo wcześniej - na każdy z etapów będzie osobne zlecenie
- możesz szczegółowo rozpisać operacje do wykonania, ale raportować produkcję zbiorczo fragmentami np. wg działu, tak dzieląc technologię, by każdy dział miał osobną technologię na komponent
- możesz przekazać zarządzanie poszczególnymi etapami produkcji różnym pracownikom - np. każdy kierownik swojego działu planuje swoje zlecenia, czyli panuje nad organizacją etapu realizowanego na swoim dziale
W jaki sposób wygenerować zlecenia na komponenty? Możesz je wygenerować ręcznie lub zlecić wygenerowanie nam. Zacznijmy od generowania ręcznego. Wykorzystasz tutaj pokrycie zapotrzebowania. W zleceniu produkcyjnym kliknij przycisk
Pokrycie zapotrzebowania, ustaw daty, wygeneruj pokrycie i kliknij przycisk
Generuj zlecenia. Jeśli na liście produktów potrzebnych do realizacji są komponenty i ich stan magazynowy na moment rozpoczęcia zlecenia głównego nie jest wystarczający zostaną założone odpowiednie zlecenia.
Z poziomu pokrycia zapotrzebowania zlecenia na komponenty zostaną utworzone tylko wtedy, gdy ich stan magazynowy nie będzie wystarczający. Jeśli natomiast zależy Ci na tym, by zlecenia te były generowane każdorazowo, niezależnie od stanu, użyj do generowania opcji
Zlecenia na komponenty. Po wejściu do okna kliknij przycisk
Generuj zlecenia na komponenty.
Wygenerowane zlecenia na komponenty będą ze sobą powiązane. Numery zleceń mają taki sam początek, jak zlecenie główne, a za pomocą przyrostka dodajemy informację z jakiego poziomu drzewa technologii powstało.
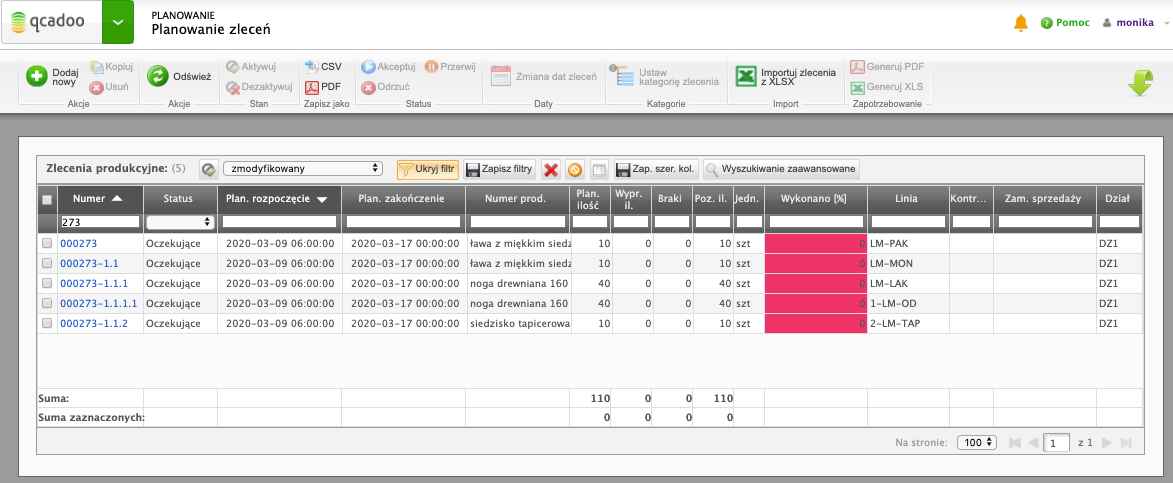
Dodanie zlecenie przez dodanie grupy zleceń do zamówienia sprzedaży
O grupach zleceń szeroko prawi ta dokumentacja - wspomnę tu tylko, że grupy zleceń przydają się, gdy produkujesz wiele bardzo podobnych produktów, np. różniących się rozmiarem, na raz. Pracownik dostaje informacje o tym co wyprodukować łącznie, na jednej kartce i nie musi szukać podobnych produktów po wielu przypisanych mu zleceniach.
Tworzenie zleceń poprzez import z akrusza Excel
Z importem danych z pliku .xlsx spotkałeś się w qcadoo już w kilku miejscach (np. przy tworzeniu produktów, pracowników, czy stacji roboczych). I tutaj zasada działania jest taka sama - po szczegóły odsyłam do tej dokumentacji.
Aby zaimportować zlecenia wejdź w Planowanie > Planowanie zleceń i kliknij przycisk
Importuj zlecenia z .xlsx. Zacznij od pobrania szablonu i wypełnienia go damymi. Koniecznie wypełnij dwie pierwsze kolumny:
- produkt (kolumna A) - podaj numer produktu zdefiniowanego w qcadoo,
- ilość (kolumna B) - podaj ilość wyrażoną w jednostce podstawowej produktu. W komórce musi znaleźć się wartość liczbowa.
Ponadto możesz uzupełnić następujące kolumny:
- numer (kolumna C) - jeśli nie podasz numeru, nadamy go za Ciebie (będzie to kolejny numer zlecenia). Jeśli chcesz podać swoje numery, pamiętaj, by były one unikalne,
- nazwa (kolumna D) - jeśli nie podasz nazwy, nadamy ją za Ciebie na podstawie informacji o produkcie, technologii i dacie utworzenia,
- opis (kolumna E) - jeśli parametry qcadoo na to wskazują, opis może zostać z automatu uzupełniony na podstawie opisu technologii,
- kontrahent (kolumna F) - podaj numer firmy zdefiniowanej w qcadoo,
- data rozpoczęcia (kolumna G) - podaj datę i godzinę rozpoczęcia zlecenia (np. 2020-05-11 06:00:00),
- data zakończenia (kolumna H) - podaj datę i godzinę planowanego zakończenia zlecenia (np. 2020-05-11 14:00:00). Data zakończenia musi być późniejsza od daty rozpoczęcia,
- termin ostateczny (kolumna I) - podaj datę i godzinę maksymalnego zakończenia zlecenia (np. terminu, na który umówiłeś się z klientem),
- technologia (kolumna J) - podaj numer technologii zdefiniowanej w qcadoo. Pamiętaj, że musi być to zaakceptowana technologia podanego produktu. Jeśli nie podasz technologii, to uzupełnimy jego domyślną technologię.
- kategoria (kolumna K) - podaj wartość ze słownika kategorii zleceń
- dział (kolumna L) - podaj numer działu zdefiniowanego w qcadoo. Jeśli dział nie będzie podany uzupełnimy go na podstawie działu uzupełnionego w technologii,
- linia (kolumna M) - podaj numer linii produkcyjnej zdefiniowanej w qcadoo. Jeśli nie podasz linii to uzupełnimy ją na podstawie linii podanej w technologii. A jeśli tam będzie pusto - pobierzemy linię w parametrów.
Tak przygotowany plik zaciągnij do qcadoo. Wszystkie utworzone zlecenia otrzymają status Oczekujące.
Ustalanie dat realizacji zlecenia
Każde zlecenie produkcyjne musi mieć określone daty realizacji - musimy wiedzieć kiedy planujesz rozpocząć i skończyć prace. Możesz daty określić ręcznie bazując na swoim doświadczeniu. Możesz też skorzystać z pomocy funkcji qcadoo, które pomogą Ci w tym zakresie.
Pierwsza pomoc dotyczyć będzie ustawienia daty rozpoczęcia - zaznacz parametr Podpowiadaj datę rozpoczęcia zlecenia przy tworzeniu zlecenia i wskaż na podstawie czego data ma być ustalana, a w momencie zapisu, gdy pole z datą będzie puste, uzupełnimy albo datę aktualną, albo datę rozpoczęcia pracy w następnym dniu roboczym, albo datę zakończenia ostatniego zlecenia na tej linii.
Data rozpoczęcia może też przenieść się z zamówienia sprzedaży - jeśli będziesz korzystać z opcji generowania zleceń do zamówienia.
Czas na ustalenie daty zakończenia.
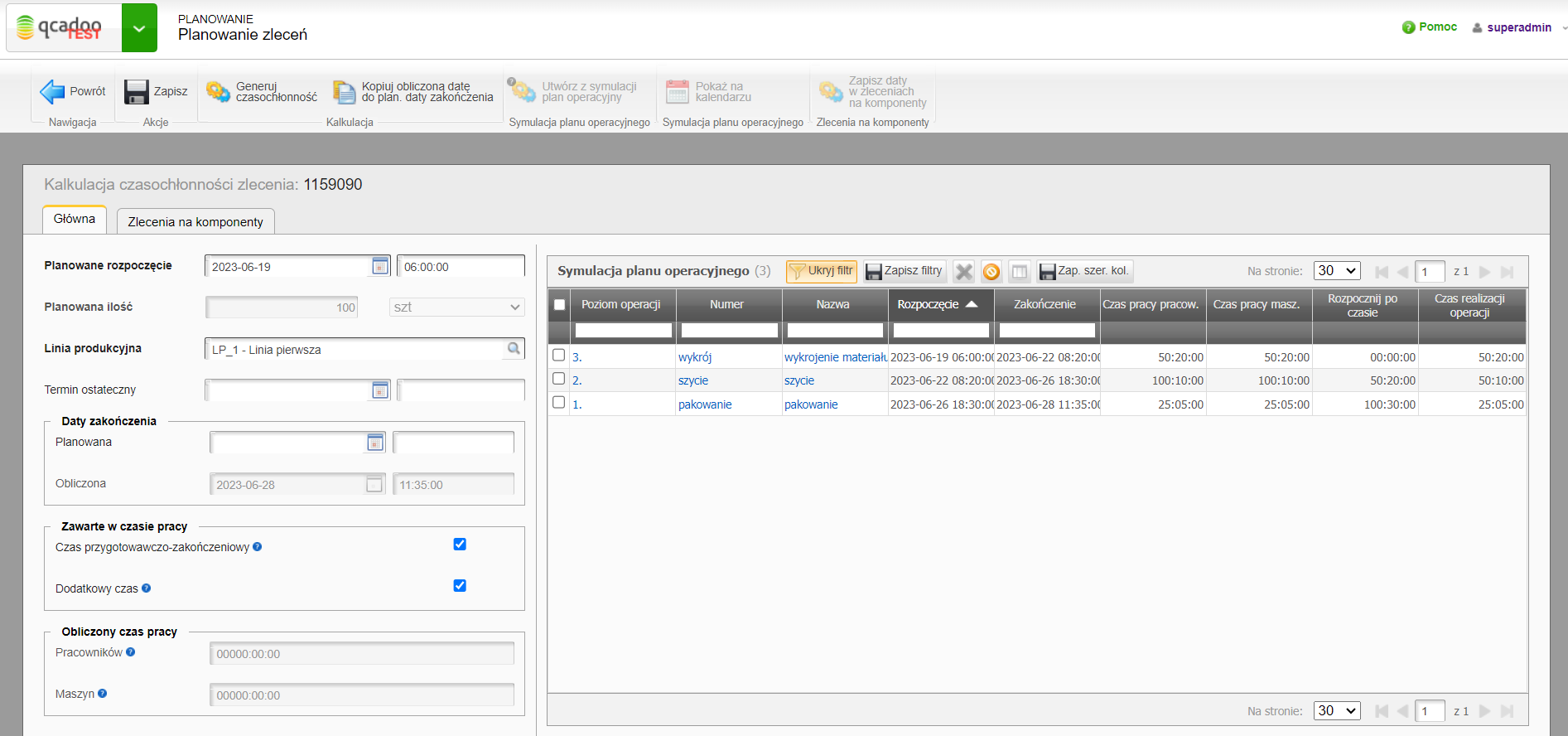
Pierwszym sposobem jest skorzystanie z kalkulacji czasochłonności. Funkcja na podstawie zdefiniowanych norm czasowych w operacji technologii wyznaczy czas trwania zlecenia, od podanej przez Ciebie daty rozpoczęcia (wyznaczając tym samym datę zakończenia).
Aby uruchomić funkcję kliknij w zleceniu przycisk
Czasochłonność
i wywołaj generowanie przyciskiem
Generuj czasochłonność. Czas każdej operacji i data zakończenia zostaną wyliczona. Wybierz
Kopiuj obliczoną datę do planowanej daty zakończenia, a wynik obliczenia pojawi się w “Planowanej dacie zakończenia”.
Kalkulacja czasochłonności może też wyliczyć daty we wszystkich powiązanych zleceniach na komponenty. W tym celu:
- wygeneruj najpierw zlecenia na komponenty
- wygeneruj kalkulację z zaznaczonym parametrem Uwzględnij zlecenia na komponenty w zakładce Zlecenia na komponenty. Daty zostaną zaktualizowane po kliknięciu przycisku
Zapisz daty w zleceniach na komponenty.
Alternatywą do wyliczenia czasu przez czasochłonność jest rozplanowanie produkcji na zmianę, a przez to wyliczenie daty zakończenia zlecenia. Natomiast jeśli zdecydowałeś się na raportowanie z dokładnością do operacji, możesz skorzystać z planowania na stację roboczą i pracownika.
Ponadto pomocnym przy wyznaczaniu dat realizacji będzie wykres Gantta.
Dodatkowe możliwości konfiguracji zlecenia
Zapewne zwróciłeś uwagę, że w zleceniu produkcyjnym jest bardzo dużo zakładek i funkcji na pasku narzędziowym. Z tego rozdziału dowiesz się do czego mogą Ci być potrzebne.
-
zakładka Daty - daty w zleceniu produkcyjnym mogą zmieniać się na każdym etapie życia zlecenia - zarówno podczas ustalania warunków produkcji, jak już po akceptacji, czy nawet już po rozpoczęciu prac. W zakładce Główna widzisz aktualne daty. W zakładce Daty zobaczysz jak wyglądały modyfikacje. Oprócz analizy zmian dat możesz zostawiać tu przyczyny zmian (a nawet wymusić ich zostawianie odpowiednio ustawiając parametry). W tym temacie zerknij też w raport odchyleń planu.
- zakładka Ilość produktu - w zakładce Główna widzisz aktualną ilość planowaną. Jeśli już po akceptacji zlecenia ilość była zmieniana zobaczysz ją jako ilość skorygowaną. Przy zmianie, podobnie jak w przypadku dat, można zostawić przyczynę korekty.
Ponadto w zakładce widać:
- zatwierdzoną produkcję (ilość wyprodukowaną z zaakceptowanych rekordów rejestracji)
- zaraportowaną produkcję (ilość wyprodukowaną z zaakceptowanych i szkicowych rekordów rejestracji)
- jaki jest procent wykonania
- ile zarejestrowano wyprodukowanych braków
- ile pozostało jeszcze do wyprodukowania
-
zakładka Zamówienie sprzedaży - zobaczysz tutaj z jakim zamówieniem sprzedaży dane zlecenie jest powiązane. Możesz tu również odłączyć zlecenie od zamówienia, czy spiąć je z zamówieniem.
-
zakładka Powiązane zlecenia - w tabeli zobaczysz wszytkie powiązane zlecenia na komponenty
- przycisk Parametry zlecenia - a w nim następujące zakładki:
- zakładka Rejestracja - większość z ustawianych tu parametrów jest powieleniem parametrów z administracji. Najważniejszy jest sposób rejestracji produkcji - oprócz tego, czy przy rejestracji będzie trzeba odnosić się do każdej operacji czy do całego zlecenia, decyduje również o podejściu do planowania. Jeśli chcesz planować całe zlecenia (na jedną linię/maszynę) i pozwolić na ich wybór w terminalu - ustaw zbiorczy sposób rejestracji. Jeśli ważne jest aby rozbić zlecenie na operacje, każdą z operacji przypisać do właściwej maszyny i pozwolić na wybór w terminalu zadania operacyjnego - ustaw rejestrację do każdej operacji.
- zakładka Magazyn - surowce - jeśli chcesz uruchamiać produkcję dopiero wtedy, gdy wszystkie surowce będą dostępne, to odznacz parametr. Nie pozwolimy wówczas zaakceptować zlecenia, gdy stany nie będą wystarczające.
- przycisk Przezbrojenia - jeśli na podstawie zdefiniowanych norm wynika, że przed rozpoczęciem zlecenia konieczne jest przezbrojenie linii, to taka informacja będzie dostępna pod tym przyciskiem.
- przycisk Technologia - przenosi do szczegółów technologii użytej w tym zleceniu
-
przycisk Utwórz zadania operacyjne - jeśli zależy Ci na tym aby pracownicy wybierali w terminalu zadania do wykonania, ale nie chcesz wykonywać planowania na stację roboczą i pracownika, możesz pójść na skróty - kliknij przycisk, a do każdej operacji z technologii zostanie założone zadanie operacyjne. Jeśli do operacji przypisana jest tylko jedna stacja - to zostanie ona w zadaniu uzupełniona. Jeśli stacja ma domyślnego pracownika - on również będzie do zadania przekazany. Pamiętaj, że funkcja możliwa do wywołania dla zleceń zaakceptowanych z rejestracją do każdej operacji. Jeśli chcesz, aby zadania tworzyły się z automatu, zaznacz parametr Automatycznie generuj zadania do zlecenia produkcyjnego.
-
przycisk Pokaż zadania operacyjne - pozwala na przeanalizowanie zadań operacyjnych powiązanych z danym zleceniem produkcyjnym. Zadania operacyjne opisane są tutaj
-
przycisk Pokaż przestoje - przycisk uruchamia listę przestojów zaewidencjonowanych do tego zlecenia.
-
przycisk Ilości wyprodukowane/użyte - w momencie akceptacji zlecenia produkcyjnego tworzy się jego szczegółowe zapotrzebowanie - czyli szczegółowo rozpisywana jest lista potrzebnych produktów do zlecenia oraz produktów, które będą efektem Twojej pracy. Podstawą do wygenerowania szczegółowego zapotrzebowania jest technologia. Od momentu akceptacji zlecenia technologia jest nie do zmiany - teraz wszelkie modyfikacje produktowe (np. wprowadzenie zamiennika) możesz przeprowadzać z tego poziomu. Funkcjonalność przyda się również do analizy zaraportowanego zużycia czy wyprodukowania każdego z produktów w procesie. Ze szczegółami działania zapoznasz się w tej dokumentacji.
-
przycisk Czasochłonność - funkcjonalność opisana na etapie wyznaczania czasów realizacji zlecenia
- przycisk Ceny i koszty - skorzystasz z niego po to, by ustalić koszty materiałowe zlecenia. Przeanalizujesz tutaj: ostatnią cenę zakupu, cenę średnio ważoną czy przyjęty koszt nominalny. Ponadto:
- dowiesz się jakie konkretne dokumenty RW zostały wystawione do zlecenia, o jakich partiach i jakich cenach
- wyliczymy dla Ciebie TKW
- dodasz lub uaktualnisz w zleceniu dodatkowe koszty bezpośrednie, zwiększające koszty całkowite zlecenia
Po stworzeniu zlecenia, wszystkie aktualne koszty bezpośrednie powiązane z technologią zostaną przekazane do zlecenia. Wartości kosztów zostaną dobrane na podstawie daty rozpoczęcia zlecenia, która wyznaczy obowiązujący aktualny koszt w tej konkretnej dacie. Z poziomu zlecenia masz również możliwość dodawnia, edycji oraz usuwania kosztów bezpośrednich.
Koszty bezpośrednie
- dodasz lub podejrzysz koszty usług obcych, czyli koszty podwykonawstwa zadań w zleceniu na usługi
-
przycisk Produkcja na zmianę - daje możliwość rozplanowania produkcji ilości zleconej na kolejne zmiany. Do wykorzystania w firmach produkujących seryjnie, z dającą się wyliczyć na podstawie norm, wydajnością danej linii. Dokładniejsze wyjaśnienia i instrukcję znajdziesz tutaj.
-
przycisk Śledzenie partii - jedno słowo - traceability. Chcesz więcej? Odsyłam do dokumentacji.
-
przycisk Dostępność surowców - pozwala na analizę stanów magazynowych surowców potrzebnych do produkcji. Sprawdzisz stan na magazynach, z których zaplanowano rozchód, ale też na pozostałych magazynach zakładu - na wypadek, gdyby trzeba było produktu poszukiwać. Możesz z tego miejsca przejść też do listy zasobów na magazynie. Dzięki temu ustalisz szczegóły jak: dostępne partie, lokalizacja (miejsca składowania), data ważności zasobów itp.
-
przycisk Wydania wewnętrzne - temat wydań wewnętrznych omówiony jest tutaj. Z tego poziomu możesz zobaczyć wydania utworzone dla danego zlecenia
- przycisk Pokrycie zapotrzebowania - umożliwa:
- ustalenie jakie surowce i komponenty będą potrzebne do produkcji
- sprawdzenie, czy w momencie planowanego rozpoczęcia zlecenia produkty będą dostępne na magazynie (funkcjonalność analizuje nie tylko dane zlecenie, ale też inne otwarte zlecenia korzystające z danych produktów)
- uzyskanie informacji o planowanych dostawach na potrzebne produkty
- złożenie zamówienia dostawy na brakujące surowce
- wygenerowanie zleceń, do komponentów z niewystarczającym stanem magazynowym
- ustalenie stanu magazynowego zamienników Po więcej odsyłam do tej dokumentacji.
- przycisk Zlecenia na komponenty - jeśli zaplanowane w technologii komponenty chcesz produkować zawsze (niezależnie od tego, czy są na magazynie, czy nie), to do generowania zleceń na komponenty wybierz tą funkcjonalność.
Ponadto z listy zleceń możesz wygenerować: zapotrzebowanie materiałowe i karty pracy.
Uruchamianie zlecenia i przekazywanie szczegółów na produkcję
O tym na jakim etapie prac ze zleceniem jesteś świadczą jego statusy. Jeśli uznasz, że masz wszystko skofigurowane jak należy - zaakceptuj zlecenie. Jeśli prace na produkcji zaczynają się lub mają się wkrótce zacząć - rozpocznij je. I to właśnie ustawianie statusu na rozpoczęcie świadczy o uruchomieniu zlecenia. Od teraz będzie ono widoczne w terminalu i będzie można do niego raportować produkcję.
W jaki sposób przekazać informację pracownikom o tym co mają wykonać:
- terminal rejestracji produkcji to najlepsze źródło informacji. Przede wszystkim dlatego, że zawiera dane zawsze aktualne. Ale też dlatego, że jego obsługa nie wymaga tony papieru. W terminalu zobaczysz zarówno zlecenia produkcyjne (raportowane zbiorczo) jak i zadania operacyjne (czyli interpretacje operacji zlecenia raportowanego z dokładnością do operacji).
- karty pracy - dostępne są dwa szablony wydruku. Dodatkowo możliwa jest ich konfiguracja w parametrach.
- wyeksportowana lista zleceń - poukrywaj zbędne kolumny i przerzuć dane go Excela lub PDFa, i w takiej formie przekaż dane pracownikom
- Gantt - daj pracownikom dostęp do qcadoo i pokaż jak działa planowanie na liniach (jeśli planujesz całe zlecenia) lub Gantt zadań operacyjnych (jeśli planujesz każdą operację do wykonania)
- dashboard - wskaż w parametrach czy chcesz widzieć zadania czy zlecenia i zdecyduj którzy użytkownicy mają mieć dostęp pełen (łącznie z edycją zlecenia), a którzy w formie ograniczonej (tylko z przesuwaniem między obszarami, przejściem do terminala i wydrukiem etykiet).
Efekty raportowania wykonanej produkcji
Efekty produkcji powinny być raportowane w qcadoo - albo korzystając z terminala, albo z rekordów rejestracji. Akceptacja meldunku uzupełnia informacje w zleceniu o ilości wyprodukowanej i brakach, oraz przelicza:
- ilość pozostałą do wyprodukowania
- procent wykonania (i oznacza komórkę kolorem, tak byś na pierwszy rzut oka mógł ocenić, czy zlecenie zostało wykonane w pełni)
Dzięki temu na bieżąco możesz monitorować postęp produkcji.